Quality Control in Custom Printing: A Comprehensive Guide
In today’s competitive market, custom printing has become an essential service for businesses looking to promote their brand, package their products, or create unique merchandise. From product packaging and business cards to t-shirts and signage, printed materials leave a lasting impression on customers. But for that impression to be positive, consistent, high-quality printing is non-negotiable. That’s where quality control (QC) plays a central role — making sure that every printed product meets the required standards before it reaches the client.
This guide takes a detailed look at how quality control works in custom printing, why it matters, and how each stage contributes to achieving flawless results.
Why Quality Control Matters in Custom Printing
Custom printing involves a delicate balance of design, color accuracy, material quality, and finishing precision. Unlike mass-production printing where every piece is identical, custom projects often involve unique sizes, styles, and designs. As a result, even minor errors can cause delays, wasted resources, increased costs, and dissatisfied clients.
Effective quality control is crucial because it ensures:
* Accurate color reproduction and matching
* Clear, sharp images and text
* Consistent sizing, alignment, and positioning
* Flawless finishing and packaging
* Timely detection and correction of errors
By implementing thorough quality checks, businesses can improve efficiency, reduce complaints, avoid costly reprints, and protect their brand reputation.
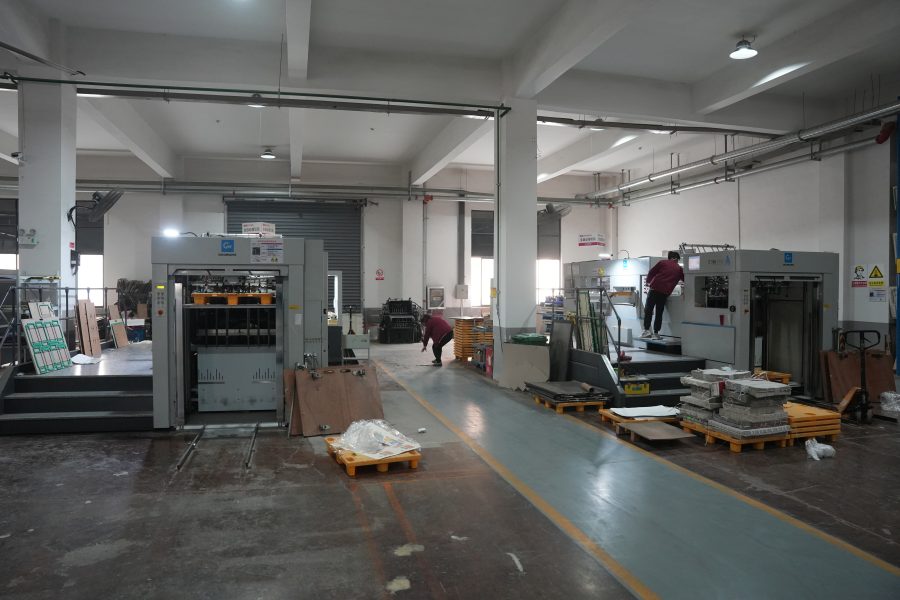
Key Stages of Quality Control in Custom Printing
To maintain high standards, quality control procedures are applied at multiple stages throughout the printing process — each focusing on specific elements that contribute to the final product’s success.
✅ 1. Pre-Press Inspection
Quality control starts before the printer is even turned on. In the pre-press stage, customer-provided design files are carefully reviewed to ensure they are print-ready. This is one of the most important phases since errors here can affect the entire job.
The pre-press inspection includes:
* Checking file resolution (usually 300 DPI for print projects)
* Verifying color modes (CMYK for print vs. RGB for digital)
* Ensuring correct bleed areas, trim lines, and margins
* Inspecting image clarity and font embedding
* Confirming layout alignment and positioning
By catching errors in this stage, printers can avoid costly rework and keep the production schedule on track.
✅ 2. Material and Ink Quality Check
Once the design files are approved, the next step is to inspect the materials and inks that will be used in the job. The selection of proper materials — whether paper, vinyl, fabric, or specialty substrates — directly impacts print quality, durability, and appearance.
Key considerations in this step:
* Surface texture and smoothness
* Material weight, color, and durability
* Ink compatibility with the material
* Color consistency and vibrancy of inks
High-quality materials and inks are essential for achieving professional, long-lasting results that meet customer expectations.
✅ 3. Proofing
Proofing acts as a bridge between the design and full production. A proof is a sample print that allows both the printer and the client to preview the final outcome before proceeding to the complete print run.
Proofing ensures:
* Accurate color reproduction
* Correct text placement and font rendering
* Proper image alignment and clarity
* Appropriate size, layout, and trim lines
If any issues are identified during this step, adjustments can be made before the job moves into mass production. This minimizes risk and increases confidence in the final product.
✅ 4. On-Press Quality Monitoring
During the print run, continuous on-press quality checks are performed to maintain consistency from the first to the last copy. Even the best-prepared files and materials can experience issues once printing begins, which is why active monitoring is critical.
Common checks include:
* Color consistency across sheets or batches
* Ink density and saturation
* Print registration (alignment of layers and colors)
* Detection of streaks, smudges, or blurred areas
Some advanced printing machines feature automatic sensors and real-time adjustment capabilities, reducing human error and ensuring precision throughout the production process.
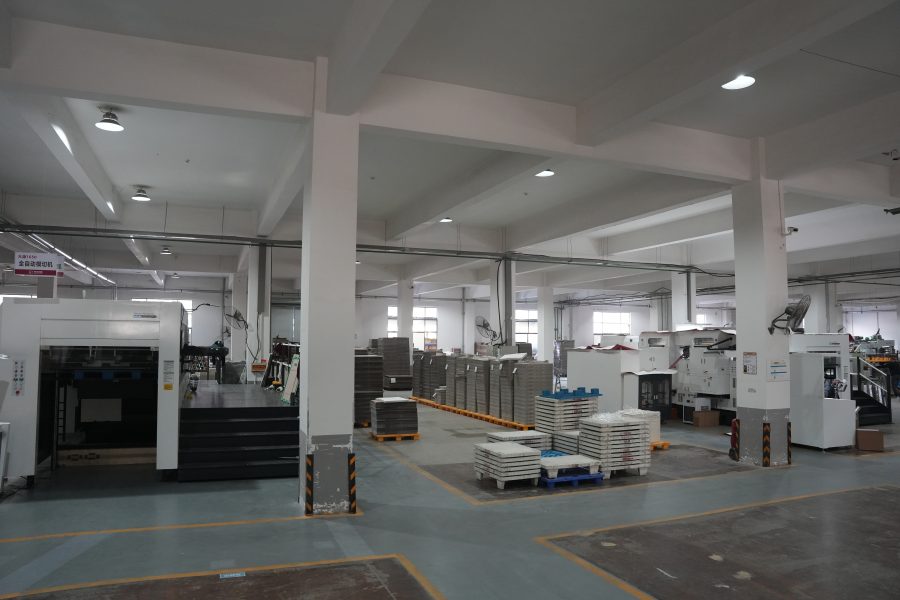
✅ 5. Post-Press Quality Check
After printing, the product often goes through post-press operations such as cutting, folding, laminating, binding, or packaging. This is another critical area for quality control, as the final appearance and functionality of the product depend on these finishing steps.
This phase includes:
* Checking cuts, trims, folds, and perforations
* Inspecting finishing applications like gloss, matte, or UV coatings
* Verifying binding, laminating, or die-cut shapes
* Ensuring correct packaging, labeling, and order details
A final product inspection ensures everything meets the client’s specifications before delivery.
Tools and Methods for Quality Control
To maintain these high standards, printers rely on specialized tools and industry practices:
* Densitometers and Spectrophotometers for measuring ink density and color accuracy
* Magnifying Loupes to inspect fine print details
* Color Proofing Software for simulating final outputs
* Sample Pulling and Random Inspections to verify consistency during the print run
* ISO Printing Standards to follow internationally accepted quality benchmarks
By combining these tools with skilled human oversight, printers can deliver precise, reliable results.
Conclusion
Quality control in custom printing is not just a process — it’s a philosophy built into every stage of production. From file preparation to packaging, every step must be managed with care, accuracy, and attention to detail. A strong QC system ensures consistent colors, clean finishes, proper alignment, and satisfied customers.
For businesses that rely on printed materials to represent their brand, effective quality control is the key to reducing errors, avoiding unnecessary costs, and building a reputation for reliability and professionalism.
By understanding and implementing these quality control practices, custom printers can confidently deliver products that look great, feel professional, and perform exactly as intended.